Virginia foundry one of only three left in America
January 2023
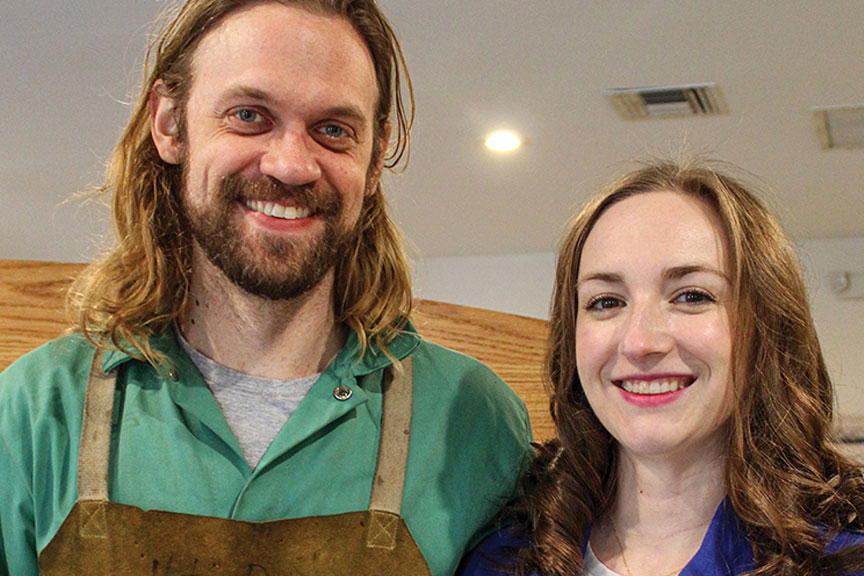
Ben and Kate Sunderlin
by Audrey Hingley, Contributing Writer
Looks can be deceiving. B.A. Sunderlin Bellfoundry is housed in a nondescript 11,000-square-foot brick building in an industrial area of Caroline County’s rural Ruther Glen. Venture inside and things are different: a custom-built 10,000-lb. mobile carillon on wheels is the lobby centerpiece. The rear foundry area, where hard work merges with creativity, is the center of the seven-employee business with a back-to-the-future approach.
Founded in 2015 by Ben and Kate Sunderlin, the foundry is only one of three remaining American bell foundries. The Sunderlins say they are the only ones utilizing traditional “swept loam” handcrafted methodology that dates back centuries.
A LOAM-LY PROFESSION
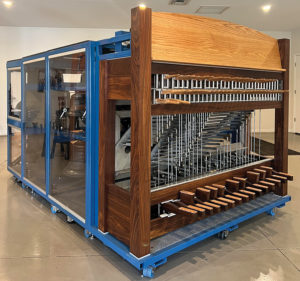
The mobile carillon at Sunderlin
Bellfoundry consists of 48 bells and is
the only one in North America.
“Loam is how traditional European foundries make bells — with clay, sand, and some sort of fibrous material like hair and manure,” Ben explains.
“Nontraditional foundries use sand and resin. Loam gives you more control over how you make the mold [for bells] and will not work in high-production volume [facilities].”
Bell molds are made in two parts: a bell-shaped core covered with a loam layer is “swept” using a template to form the inside of the bell while the outer part, or cope, is also lined with loam, the two sides pressed together before the bell is cast. Bell metal, an 80% copper and 20% tin mixture, is fired in the foundry furnace, where temperatures rise to 2,000 degrees before the hot bronze mixture can be “poured over” into the bell mold.
The custom process is painstaking and not cheap: bell metal is about $9 per pound, so raw materials alone can increase prices.Human hair used in the traditional loam recipe comes from floor sweepings donated by a local salon. For free manure, Ben explains, “We muck out local stables.Hair is only used in some loam recipes but horse manure is used regularly so we need to muck every two months.”
Customers include churches, colleges and municipalities; recently Sunderlin was awarded a Virginia Tourism Corporation Microbusiness marketing grant. Past projects include Historic Jamestowne’s Memorial Church replica bell and a 55-bell carillon at NC State University’s Memorial Tower. One current project is carillon restoration for the original Minnesota Mayo Clinic; another is a 10-bell chime for Richmond’s Grace & Holy Trinity Episcopal Church.
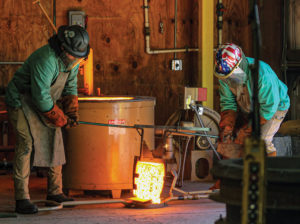
Employees Christian Goff and Mark Darlington
move a crucible from the furnace to the shank.
“We have a tower, and structural modifications are being done to house the bells,” says choirmaster and organist Dr. ElizabethMelcher Davis. “We wanted bells of high quality that would be long-lasting. It will play peals, tolls, Westminster chimes and hymns.We were able to go onsite and watch our bells being poured.”
WEDDING BELLS
Kate, who grew up in Chesapeake, Va., and Ben, who hails from Lafayette, Indiana, met at Notre Dame University where they were pursuing master’s degrees in art and art history, respectively. Ben had enrolled in Indianapolis’ Herron School of Art after high school, where his fascination with bells and campanology (the study of bells) began. Research grants allowed him to study traditional bell making in several European countries.The two wound up in Virginia after Kate was accepted into Virginia Commonwealth University’s Ph.D. art history program. “I joke I got into it [bell making] because of Ben.We have a marriage but there’s also a marriage [regarding business],” Kate says.
Parenthood sidelined Kate’s studies; she’s in the final year of her Ph.D. program, with daughters Jane, 4, and Elizabeth, 20 months. Juggling motherhood with working alongside Ben, she also hosts by-appointment-only foundry tours where visitors learn about the art, science and history of making bells.
Kate, who once aspired to work in a museum, laughs, “Who knew the museum would be our own?” Ben says, “I am an artist who fell in love with foundry work. Not a lot of people understand that people still do this.”